CHP Operation – Financial and Carbon Savings – Webinar
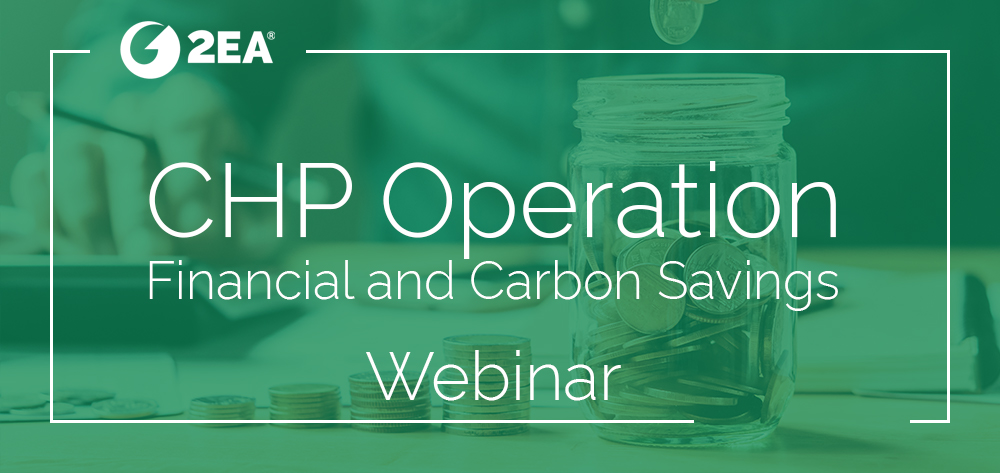
- Download Andrew Gardner’s Presentation
- Download Chris Marsden’s Presentation
- View Questions and Answers
- CCL Calculator
- CHP Services
- CCL Cost Analysis Paper
On Monday 18th May, Andrew Gardner of 2EA, in conjunction with Chris Marsland and CIBSE Certification Ltd, took part in a webinar on Combined Heat and Power (CHP) operations, looking at both financial and carbon savings.
This webinar explains CHP technology and provides useful examples from a real-building case study to illustrate how you can calculate both the financial and carbon benefits of operating a CHP unit.
This webinar includes:
- A look at Climate Change Levy (CCL)
- A look at the CHPQA Programme
- Understanding and calculating CHP running costs
- Understanding and calculating CHP electricity savings
- Understanding and calculating CHP heat savings
- Understanding what a CHP is
- Understanding what a CHP does
- The correct CHP sizing
- The benefits to a site of having a CHP unit
- The pitfalls to consider
- A comparison to other systems
Please see the video of the webinar and full transcription below:
Video Transcription
Andrew Geens: Good afternoon everyone, this is Andrew Geens from CIBSE Certification here to introduce what is our only webinar for May. So welcome everyone to our May webinar. We have two webinars lined up for June so keep an eye on your inboxes for information on those.
We have two speakers today; Chris Marsland and Andrew Gardner. I’m going to leave it to them to introduce themselves. They’ll tell you the parts of the presentation they’re dealing with. You’ve all seen the flyer for this webinar which is why you’re here. I was toying with the idea of calling it “All we wanted to know about CHP but we’re afraid to ask” but we’d probably get a rip from Woody Allen if I did that. So I will just hand you over straight away to our first presenter Chris Marsland, over to you Chris.
Chris Marsden from CIBSE Certification
Chris Marsden: Good afternoon everyone, thank you, Andrew, for the introduction. Just to set a little bit of a background, I’ve been in the CHP industry since 1998, worked for a couple of different providers and been responsible for some of the design, installation and remote monitoring of CHP’s during those 20 odd years. I’ve also sat on some industry bodies both the ADE, Energy UK and also on some BSI committees. So I hope I’ve got a reasonable level of background understanding that I can endeavour to get across to you today and there are some questions and answers later and I’d be really pleased to take any questions from you at that point of time.
Energy savings
So I think before we go too far into this webinar it’s good to remind ourselves of the underlying premise of combined heat and power. Some of you will have seen this type of high-level Sankey diagram before so please bear with me. As you can see on the left-hand side of this graphic, with conventional electricity generation there’s a poor conversion efficiency. This is not just caused by the waste heat from the power plant but also by the transmission losses from the large centralized plant.
The heat generation efficiency, whilst typically more under your control, can still be bad. We’ve all been to sites where the boilers are old and inefficient or simply not very well integrated. Many older sites will be happy to achieve a 75% boiler efficiency that’s shown on this diagram. These factors can lead to an overall energy efficiency of less than 60 percent. Turning our attention to the right-hand graphic, we can see that the simultaneous generation of electricity and heat in the combined heat and power unit can bring this conversion efficiency up to around 85%, allowing you to get the most from the fuel and reducing waste, something that is vital for all modern businesses.
How CHP works
It’s not essential to know the innermost workings of a combined heat and power unit, it can be treated like a black box but as an engineer, I always like to try and gain at least a rudimentary handle on any technology I work with.
So here we have a stylized representation of the main components of a combined heat and power unit. Starting on the left-hand side you can see the prime mover, typically a diesel engine converted to run on gas, most of the time natural gas, this drives the generator to produce the electricity for the site. It’s important to emphasize here that there’s no switching involved unlike with standby diesel generator sets.
The cables from the combined heat and power unit are connected in parallel with the incoming power from the utility. The laws of physics mean that the energy generated locally is consumed first with the utility seamlessly topping up to match the energy required by the site. Thermal energy is recovered from the engine jacket and from the exhaust gases using an exhaust gas heat exchanger.
This is typically a shell and tube heat exchanger where the water flows around tubes that the exhaust gases flow. In this model, the thermal energy is shown being recovered as low-temperature hot water but this can be medium temperature, hot water a mixture of hot water and steam or even chilled water but I don’t intend to get into that level of detail in this webinar.
Simple boiler interface
Assuming the site is using the thermal energy as hot water there are several ways to link this into the system. I’ve shown here the most simple form, a series interface. There are many other ways to connect to a combined heat and power unit. The next most common is the parallel interface and then those utilizing a thermal store but the series connection in my opinion is the easiest and the best.
As you can see here, the combined heat and power unit is taking a proportion of the cooler returned water and heating it up prior to mixing it with the rest of the returned water before it goes onto the existing bank of boilers.
One of the main advantages of this type of interface is that the combined heat and power unit is always the lead boiler by a virtue of it seeing the coldest water first. One of the biggest problems I see in combined heat and power unit installations is that the combined heat and power unit is not treated as the lead boiler, thus it cycles and upsets all the sizing and modeling that is the key to the economic success of a combined heat and power installation. This configuration also means the need for a BMS control system is virtually non-existent, making it simple and foolproof and ideal for older buildings without a large BMS system.
CHP key design issues
So let’s for a moment think about how to pick the right size combined heat and power unit for your building. These first three points can seem like common sense but in my time I’ve seen plenty of examples where these points have not been properly considered and have led to dissatisfied customers with an investment that is not providing the promised returns. I’ll come back to these three points in the next slide, but I cannot emphasize enough how important it is that as much of the heat as possible is utilized.
As we saw earlier in the inclusion of the co-generating heat that gives us the large combined efficiency of the combined heat and power unit. There can be a temptation to put the biggest combined heat and power unit into the site based upon the peak electrical demand but that will be wrong. It is a careful balancing act that needs thoughtful modeling and a deep understanding of the site’s operational energy profile to ensure the best fit, again, more later. Finally for this slide we mustn’t forget the electrical side of things, whilst the electrical connection is often less complicated than the water connection and many traders refer to this as “running a piece of wet string” – it can sometimes be challenging to find routes for cables. Cables which grow in size and cost the longer the run required.
Demand profile requirements
To size a combined heat and power unit correctly, we have to consider both the thermal and electrical load profiles. It is typically the thermal load that is assessed first as this is usually the factor that limits the combined heat and power units size. If the site cannot consume the heat then the combined heat and power unit will not operate efficiently.
Here we have a typical 12-month thermal profile for a building with a high demand in the winter months and a significant dip in demand in the summer. Against this profile there are really three common approaches to combined heat and power unit sizing.
The first is sizing to the base load. What this means is that the combined heat and power unit has been sized to run continuously against the thermal demand, the blue area on the top left graph, the system is small enough so that there is never too much heat for the needs of the building hot water and heating systems. The remaining shaded red areas will be supplied with heat from the conventional boiler plant. This approach to the sizing is very common and ensures optimum efficiency.
The second approach to thermal sizing is to size the combined heat and power units above the thermal base load as illustrated on the bottom left graph. The combined heat and power unit now has the capacity to generate excess heat in the summer represented by the pink portion of the graph. This would need to be rejected via a radiator. But it also generates more useful heat in the winter and will also have a higher electrical output than the previous example. The third approach of an operational feature in a lot of combined heat and power units known as modulation, load following all load tracking. The combined heat and power unit in the bottom right graph is sized the same as the previous graph but instead of maintaining full load output in summer and having to reject heat it modulates its output to track the thermal demand of the site.
This is a sophisticated mode of operation that relies on the combined heat and power unit having a suitable control system and, more importantly, the rate of change if the thermal load needs to be compatible with the combined heat and power units speed of response.
There is no right or wrong in these three approaches and the most immediately obvious approach is not always the approach that saves the most money for the client. It should also be borne in mind during the sizing and selection processes that the combined heat and power unit needs to be able to be classed as good quality under the government CHPQA scheme to access valuable financial benefits, but more of this later in the webinar from Andrew Gardner.
Arriving at the optimum sizing solution for any site requires detailed modeling against not only the site load profiles but also the tariffs the site is paying for his gas and electricity. As with thermal sizing the assessment of the electrical load also relies on good quality site data.
CHP sizing – The devil is in the detail!
My review of sizing in this section of the webinar has been based on fairly simple profiles that would derive from reviewing the monthly utility bills of a real potential combined heat and power unit customer.
The use of monthly data whilst the good initial screen is seldom accurate enough to truly identify how a combined heat and power unit will operate against the building or a process. These charts show the same customer’s load profiles over a specific 24 hour period using half hourly data.
As you can see, the half hourly assessment reveals the true operational behavior of the building; the load shape is markedly different to that of the monthly averages. The electrical and thermal sizing needs to look at every operational half-hour throughout the year in order to make an accurate assessment of the site’s energy requirements and thus determine the optimum combined heat and power unit size. In this case sizing the system on the profiles would have resulted in an overstatement of savings amounting to more than 30 percent.
It would also have produced significant operational difficulties including excessive heat rejection, unplanned exporting of electricity and low load system starts and stops. I think to summarize these last two slides I’d say don’t be greedy when looking for potential savings, they are there to be had, but don’t overreach yourselves.
Other factors to consider
Once the initial sizing has been worked through, there are other factors that need to be considered too. You’ll be pleased to hear I’m not going to read through all of these points but a few worthy of a little further explanation are; firstly, and this applies to many many energy-saving technologies and/or techniques, is don’t jump first to the technology to save money or make your business more energy efficient.
Look for simple causes of waste and situations where people are involved in controlling the energy. There are still lots of free opportunities to save energy by education and changing the way people and processes behave.
Secondly, gas pressure can be an issue with combined heat and power units for a couple of reasons. The obvious one is whether there is enough gas pressure on-site. Unfortunately, there is not a standard pressure requirement for combined heat and power units, however, I would use a rule of thumb that under 400 to 500 kilowatt electric 22 – 50 millibar gas pressure is okay but above that you will need 180 sometimes up to 300 millibar. Now there are always exceptions to this. Certain larger engines require small volumes of gas at pressures of several bars so always check with your chosen supplier.
Just because the site doesn’t have a gas supply at 250 milli bar doesn’t mean that a larger combined heat and power unit is out of the question. The lack of pressure can be solved by the installation of a gas booster. These are a simple solution provided the gas supply is capable of supplying the volume of gas necessary. This needs to be checked with the host site and probably then with their gas supplier as they’re unlikely to know. One way that low gas pressure can manifest itself is starvation of the combined heat and power unit on cold winters days. Pressures may have been measured or calculated when no boilers were firing or when consumption was low so on a really cold day the combined heat power unit can see reduced pressure which can cause operational problems.
Another point to note about gas is that a combined heat and power unit producing 300 kilowatts of heat, takes more gas than a boiler producing 300 kilowatts of heat. Now this might seem obvious but I have seen instances where it clearly hasn’t been. The simple rule of thumb is the gas required will be approximately three times the electric output of the combined heat power unit. Now at the risk of sounding like an advert for CIBSE, I would always recommend the excellent document AM12 developed by Paul Woods, another industry expert, some twenty years ago. This was revised about five years ago and, although some of the content is unfortunately dated now, the underlying principles and techniques are as sound today as ever.
CHP positioning
Finally, a brief look at some of the pros and cons for the choice of combined heat and power unit location. again this slide is pretty self-explanatory but I would like to take a moment to focus on the servicing aspects of combined heat and power units.
Providing good access for servicing is often overlooked and this is linked to a whole other topic that has to be considered. A combined heat and power unit needs regular maintenance. If it doesn’t or can’t run it’s just an expensive white elephant. So providing good servicing facilities and signing up for a good maintenance contract are as important to realise in the projected benefits of a combined heat and power installation as is a good quality design and install.
I don’t intend to talk about maintenance anymore in this webinar. Safe to say that there is one item missing from this chart and that is the need for oil tanks. The combined heat and power unit when it’s being serviced, just like your car, needs it’s oil changing at regular intervals and it helps to reduce service costs if a pair of local oil tanks can be provided; one for the waste oil and one for the clean oil.
I would go as far as to say that servicing of the larger units greater than 300 kilowatt electric is not really practical without the provision of such tanks. Your chosen supplier should be able to revise on the optimum tank size for your chosen combined heat and power unit. These tanks don’t necessarily need to be directly adjacent at the combined heat and power unit as they also have to have a fill point located near vehicle access for the tankers to fill and empty them.
Summary
As you have learnt in my very quick canter through some of the points that need to be considered before installing a combined heat and power unit, it can be a tricky technical business. Because of this most of the large combined heat and power unit suppliers provide free feasibility studies and have complex in-house models that take the daunting 12 months of half-hourly data and work through the many possibilities to give the optimum size for the site. I would suggest that you avail yourself of this service even if you only buy the combined heat and power unit from the supplier and install it yourselves.
CHP equipment options
So what does a combined heat and power unit look like? Well, before I get on to the next slide let me just say this, I’ve been told off in the past for referring to them as boring grey boxes. Whilst I completely accept this is being dismissive of a lot of complicated design and up-to-date technology, some of which I’ve been responsible for, this is exactly what they should be; it should be a fit and forget piece of equipment accompanied by a good maintenance contract which means that you never hear anything about the unit.
CHP options – Internal packages
Casting your minds back to the combined heat and power unit location slide earlier, let’s look at internal units first.
The unit in the picture here is a 60 kilowatt electric unit that is approximately three meters long, one meter wide and two meters high. It will weigh-in anywhere between two and three tons. The package contains everything you saw in the earlier slide: i.e. engine, generator, heat exchangers, control panel and, in some instances, exhaust silencers.
The largest unit you tend to get in this package style is around 500 kilowatt electric. These units are produced on assembly lines and can be purchased at very reasonable prices. However, because of this they tend to have limited options. Often this means that they have a fixed flow and return temperature or a fixed pumping capacity or limited control interface options. Large capacity units will tend to be built on site using a modular approach and because of this they can be better characterized to the site’s needs.
One issue with internal combined heat and power units is the high level of building integration they require. This can start with the apparently simple process for getting the unit into the building to its final installation site. Sometimes the cost of this integration can be equal to or more than the cost of the combined heat and power unit itself. Not that this is always a showstopper for a site with a good match for combined heat and power.
Where integration is either too costly or the unit is too large to fit in the building or there is suitable space available externally, an external unit should be considered.
CHP options – External packages
This unit is 200 kilowatt electric but as you can see it is significantly larger than the 60 kilowatt unit on the previous slide.
This combined heat and power unit has been constructed in a bespoke equivalent of a 20 foot shipping container. This allows all the equipment to be installed inside the secure, weatherproof and soundproof housing and allows a service engineer plenty of room to maintain the unit.
This type of construction can be used for any size unit, although it typically works best for the larger units. Units in excess of 2 megawatt electric can be packaged like this to great effect. Site integration is also much simpler and cheaper, requiring two pipes for hot water, one pipe for the gas and one cable for the electricity. An additional benefit of the reduced installation complexity is the fact that the unit can be easily moved to another site should the current site’s energy demands change.
So that’s my last slide. I want to thank you for your attention. I’ll hand back to Andrew Geens now for the rest of the webinar, thank you.
Thank you
Andrew Geens: Okay thank you very much Chris. I’m just going to change the presenter so that Andrew can continue.
Should be with you now Andrew.
Andrew Gardner from 2EA Consulting
Good afternoon. My name is Andrew Gardner, thank you, Andrew Geens. Hopefully, you should be able to see my screen which says CHP Operation, Natural and Carbon Savings Explained.
CHP operation, natural and carbon savings explained
Well welcome everybody may I just say that this is my very first webinar, so please bear with me if there are any hiccups. This part of the webinar is split into three parts; the first part will deal with Climate Change Levy and the CHPQA program, the second deals with CHP financial savings and the final part deals with CHP CO2 savings.
Who we are
So briefly, I’ve been in the industry for over 20 years. I was part of a government consultation tasked to review climate change taxation and its introduction into the UK centered around discussions on what exemptions and exclusions should apply. Further to this, I have worked on the exemptions for CHPs under the CHPQA program for which I also contributed a paper covering the feasibility of micro CHPs.
What we will be covering
So in this presentation we will be looking firstly at the role of CCL and how CHP benefits, how to obtain a CCL exemption through the CHPQA, and how to calculate CHP savings both financial and carbon.
Climate Change Levy (CCL)
So before we jump into the savings, I will quickly run through what CCL is and how CHP’s relate to it.
So CCL was proposed in the Finance Act 2000 and implemented in the 2001 budget. Effectively it is a tax on energy to reduce consumption for non domestic supply.
Here is a brief look at the CCL rates and as you can see there was a significant jump in 2018 to 2019, this is because the government abolished the Carbon Reduction Commitment or CRC and raised the rates of CCL to offset this loss.
During the 2016 budget it was announced that there would be a harmonization of the CCL rates for gas and electricity by 2025. Therefore, the government is raising the rates on gas to £0.00568 in 2022/2023 and to £0.00672 in 2023/2024 whilst freezing the rates on electricity.
So you can see the effect of these rate increases, we have compiled actual energy data from seven key sectors and the impact on the costs to business.
By owning and operating a CHP you are able to reduce these costs which brings us on to a brief overview of the CHPQA program and how you can benefit from CCL relief by installing and operating a CHP.
CHPQA programme
So let’s look at the CHPQA program in a little bit more detail.
What is the CHPQA
The Combined Heat and Power Quality Assurance Program, CHPQA, was introduced to incentivise CHP by offering additional benefits such as CCL exemption and preferential business rates. To obtain these benefits your CHP unit must be registered and certified with the program. Please note that participation is voluntary.
So this is a quick overview of the CHPQA registration process – I’ll leave this on the screen for a short period but please be aware that all the slides will be available after the webinar so you can look at them in more detail.
CHP savings
So now let’s look at the actual savings that can be made on a CHP unit.
Is your CHP unit making you savings?
When you ask CHP owners why they’re operating a CHP unit they most often answer because it saves us money. But how do you know your CHP is making you savings? Unless you know how to calculate the savings but can you be sure? and this is what we will cover in this section.
What do you need to know?
So what do we need to know? Well, before we can start calculating the savings there are two major requirements – these are the utility prices and the CHP operational data. We will deal with each in turn.
Utility prices
Utility prices: so you’ll need your electricity day rate, your electricity night rate, the gas price, the maintenance costs and the rates of climate change levy for gas and electricity. The maintenance cost is normally the rate charged by the CHP maintainer based on electricity generated by the CHP. This is also known as the CHP electricity price.
CHP operational data
CHP operational data well we’ll need to know the hours run in the period, the gas used in the period, the CHP electricity generated in the period, and heat supplied. You’ll also need to know the heat efficiency of your backup boilers. Once we have the above data we can now start calculating what your CHP savings are and this is normally done on a monthly basis.
CHP operation
So simply put, a CHP unit consumes gas to generate electricity and supply heat to the site it is installed at. These calculations we’re going to make the following assumptions with regards to the CHP operation and the utility prices. This is a relatively small-scale CHP unit most commonly found in leisure centers or hotels. we’ll also assume that the CHP operates 17 hours a day, therefore, it does not run during the night period.
So taking the month of January 2020 as an example, then the CHP unit would have operated for 527 hours and generated and consumed the following. Finally, before we start calculating the CHP savings, we must know if the CHP unit is registered under the CHPQA program as this will make a significant difference in the savings that can be made.
If the unit is registered and meets the criteria of good quality CHP, then all the gas used and all the electricity generated will be exempt from climate change levy. For this example, we will assume that the CHP unit is registered and certified as good quality.
Also for the example we will assume the following utility prices. So your electricity rate in the day, the night rate, the gas price and the maintenance cost. The climate change levy rates for 2020 in January were 339 for the gas and 847 [electricity]. We will also assume that the gas back up boiler heat efficiency is 85%.
CHP costs
First step is to calculate the CHP costs. Effectively the total cost to operate the CHP unit is the cost of the gas consumed and the cost of the maintenance to operate it. So we have for the cost of the gas 3162 and the cost of the maintenance 1581 giving us a total operational cost of £4743.
CHP savings
Now let’s look at the savings. Well savings can be separated into two parts; the electricity savings and the heat savings.
The electricity savings
So let’s deal with the electricity savings. If there was no CHP unit operating on-site then the electricity generated by the CHP would have to be imported from the grid and would include the cost of CCL. So the cost of importing the equivalent of electricity from the grid would be the day rate plus the CCL rate from electricity to give you a total electricity price.
Therefore, the total cost to import the equivalent electricity from the grid would be 4662.37. Now let’s look at the heat savings.
The heat savings
We must also take into account the heat supplied by the CHP unit. Again if this was not available, then this heat would have to be supplied by the site boilers which would use gas to generate it.
Assuming that the boiler efficiency is 85%, then the quantity of gas used to generate the equivalent heat would be as follows. So 93,000 kilowatts of gas would be needed to generate a similar amount of heat. As the gas used in the boiler is not subject to CCL exemption then the CCL rate the gas needs to be included in the gas price.
So as we did for the electricity price we have the base gas price, the CCL on gas rate which gives us a total gas price. Therefore, the total cost of the boiler gas used to replace the equivalent heat from the CHP would be £2175.27.
So this is an effective saving, as this gas does not have to be purchased to generate the heat that is being supplied by the CHP unit.
Total savings
So if we look at the total savings we’ve got the total saving on the electricity, the total heat saving which gives us a total energy saving of 6837.67. However, from this we must deduct the total CHP operational cost, which we know is 4743. Therefore, this gives us a total net monthly saving of £2,094.64.
Please note that the above example is based upon the optimum performance of the CHP unit. To calculate your actual savings the meter values for CHP electricity generated, heat supplied and gas consumed must be used.
CHP savings – The carbon
So now let’s look at the CHP carbon savings.
Is your CHP unit making carbon savings?
If operating correctly your CHP unit will also give you carbon savings, which under the current climate can just be as important as the financial savings.
In this section we look at the most common methodology to calculate your CHP carbon savings.
What do you need to know?
So what do we need to know? Well you’ll need your emissions factor, both gas electricity, and the CHP operational data.
Emissions factors
For the example shown we will be using the following emissions factors for natural gas and for electricity. Emissions factors used here are purely for example and are from the CRC for the year 2014/2015. An alternative could be the greenhouse gas emissions factors issued by the government on an annual basis.
CHP operational data
So what CHP operational data do we need? Well you’ll need the CHP gas used, CHP electricity generated and the CHP heat supplied. You will also require details of the heat efficiency of the gas fired backup boiler.
Once we have the above data for a specific period that we wish to look at, and this is normally annually, then we can start to calculate CHP carbon savings.
So using a sample year the CHP unit generated and consumed the following. We will also assume that the backup boilers heat efficiency is 80%.
CHP carbon emissions
The CHP carbon emissions. Effectively the total carbon emissions from the CHP is the total gas consumed multiplied by the emissions factor for natural gas. So in this case the emissions would be 220,435 kilos of co2.
The CHP carbon savings – Electricity
Again, as before, if there was no CHP unit operating on-site, then the electricity generated by the CHP would have to be imported from the grid and this would include carbon emissions. So the carbon emissions from importing the equivalent electricity from the grid would be this which equates to 140,607 kilos.
The CHP carbon savings – Heat
We must also take into account, as before, the heat supplied by the CHP unit as once again this heat would have to be supplied by the boilers and gas consumed by the boilers and, therefore, the equivalent boiler gas would be as shown which will give you 715,413 kilowatts of gas to generate the equivalent amount of heat. As the gas used in the boiler also creates carbon emissions, then this must also be taken into consideration when calculating your carbon savings.
So the equivalent carbon would be the boiler gas emissions times by the factor which gives you 132,035 kilos. So again this is an effective carbon saving as this gas does not have to be consumed by the boiler to generate the heat that is being supplied by the CHP.
Total carbon savings
So let’s look at the total savings.
So the CHP carbon saving on electricity is 140,607 and the savings on the heat are 132,000 which gives you a total carbon saving of 272,642. However, from this we must deduct the total emissions from the CHP which we know is 227,435 which gives us a total annual CHP carbon saving of 52,2070 kilos. this equates to a percentage saving of 19% against the equivalent consumption from the grids.
Total savings
So to summarise, your financial savings on a monthly basis would be £2,094.64 pence and your total annual carbon saving would be 52,207 kilos. So from these calculations. Based on a relatively small size CHP unit, we can see that both make significant financial savings (about £25k) a year and carbon savings about 52 tonnes a year.
Again, it is worth emphasizing that these calculations are based on ideal operational data. It is the methodology that is important to take away.
Key takeaways
So thanks for listening, I hope this made sense. We will now take questions, but before we do here’s some key takeaways when considering a CHP unit:
- Ensure your CHP unit is correctly sized for the site it is to operate on.
- For maximum efficiency, the CHP scheme should be heat led.
- Register your CHP unit with the CHPQA program
- Don’t forget to complete your HMRC forms PP10 and PP11 to obtain your CCL exemption.
- In doing so you’ll also need to carry out annual CCL reconciliation.
We also have an online CCL calculator for anyone that wants to work out CCL costs to their business as well as articles covering CHP savings calculations. Alongside this we have a paper titled “A multi-sector analysis of the cost difference off CCL rates 2018 – 2022 – this is where our figures within the CCL section of this presentation came from.
Thank you. So Andrew Geens, I hand back to you.
Questions
Andrew Geens: Okay thank you, Andrew. we’ve had a few questions come in, but before I go to questions, Andrew did say on one of his slides that the slides will be available the webinar has been recorded as well – should have said that in the introduction – both the slides and the recording will be available from the news section on our website from about tomorrow afternoon.
I’m going to try to go through the questions in the order they come in if we can answer them as quickly as possible.
Q) So the first question was: do you think CHP is suitable for every project?
I think we’ve only got Andrew available to answer that at the moment.
A) Andrew Gardner: it very much depends upon the project. CHPs can run from as little as 30 kilowatts electrical up to 2 megawatts electrical and even larger in bespoke projects.
So normally you should be able to find a CHP unit that will fit but please remember it’s the thermal load that you need to look at most of all.
Andrew Geens: Ok thanks Andrew.
I’ll combine two questions here actually:
Q) Does the lowering of carbon contents at grid electricity, in fact three questions someone, pointed out that the factor is much lower now than the figures you used an example, so does the lowering of the carbon content grid electricity mean the end of the road for CHP or is it going to have to adapt to their future you’ll be talking about things like hydrogen fuel cells for CHP.
A)Andrew Gardner: Yes the carbon factors I used were from the CRC for 2014/2015 as I said they were purely for an example. Yes, the grid factor for electricity has dropped, and it’s dropped quite a lot. However, CHP will still make you carbon savings, as for the future that is something that Chris would be probably better able to answer than myself at this time.
Andrew Geens: OK Chris can come in there. I’ve managed to reconnect him.
Chris Marsland: Thanks Andrew. yes, it certainly does make a difference I think it as with all things it’s a question of which statistics you believe.
Yes, certainly the CRC numbers in Andrews calculation were from a previous period I think the CRC note that the emission factor numbers you see currently are widely varying and also if you actually look at the instantaneous ones for this period of time when there’s a lower electrical demand on the on the National Grid, they are quite low.
However, the ADE the Association for Decentralised Energy did some work last year, beginning of last year, showing that actually CHP is currently still displacing marginal plants when it runs.
Therefore, the headline figures for grid carbon aren’t necessarily the ones you should be using. You tend to be displacing plant that’s got more carbon emissions than the average because you’re not displacing the have to runs such as nuclear and the free fuel ones such as the renewables so it’s still a very muddy picture but there is still massive value to the end customer in CHP particularly with the spark spreads that we’re seeing these days.
Andrew Geens: Thanks Chris.
Q) Another question I think for Chris, in one of your early slides you mentioned the situation where you wouldn’t need BMS, could you just clarify that please?
A) Chris Marsland: Yes absolutely, I think my point was there where you have a very simple serial connection. The CHP will run on its own time clock and because it’s seeing the cold water first it’s just preheating the water back to the boilers. It doesn’t really need any temperature control, it doesn’t really need any cycling and anything else it will look after itself and then the boilers are acting as a top-up so that there’s this very limited need for a sophisticated control system. Where you go to obviously thermal stores, there’s a need for a more sophisticated BMS type control system and even the parallel connection where the CHP, if you think about that original drawing of mine, you have the two boilers sat on the floor and returned mains there are quite a lot of installations where the CHP will be sat in parallel with the boilers on the flow and return mains and in those instances you do need a BMS type control system to ensure that the CHP is the lead boiler. But in the serial connection you really, you know, in its crudest form you can connect it up, set the time clock to run seven o’clock in the morning till midnight or whatever is appropriate and leave it be and yeah it doesn’t really need any other form of control.
Andrew Geens: Okay thanks, we’re getting questions coming in quicker than we can answer them so let’s keep moving.
Q) Is there a way to calculate the maintenance costs of a system that has yet to be installed, is there a rule of thumb for this?
A) Chris Marsland: I would say you speak to your prospective supplier. There are numbers. I mean Andrew’s put a number in his presentation which is as good as any, but it obviously depends on the type of equipment that you use, the manufacturer, the run hours – there are a lot of variables. I’m sure a decent manufacturer supplier could give you a rule of thumb for or a set of numbers for working it out.
Andrew Gardner: Absolutely and also the type of maintenance contract and how long the maintenance contract will also affect the price.
Andrew Geens: Okay thanks, Andrew.
Q) The next question is could data centres benefit from CHP, even if it’s electricity led?
Andrew Gardner: Yes, because most data centres also have a requirement for a cooling mode and so your CHP could be configured for trigeneration purposes. Chris may be able to spread a little bit more light on this.
Chris Marsland: I’m not sure I can add any more to that Andrew. Yes, absolutely, CHP for data centers is an area that’s been an area of interest for the last four, five or more years. It’s never really gained traction. I’m not a hundred percent sure why even now because, as Andrew says, there is a good balance of chilled, electric and a little bit of heat load, so yeah, it’s it’s an oddball on that one, it’s always appeared to have potential to me but has never managed to sort of break into the area or any in any sizable installation or sizeable quantity.
Andrew Geens: Okay thanks.
Q) The next one is pretty straightforward; can you generate electricity and feed into the grid?
A) Chris Marsland: Yes you can. You can have a CHP, that’s if you’ve got to think back to my original sizing screens, you can have a very large CHP provided you can use all the heat and any excess electricity can be exported back to the grid. As with all these things, it’s getting a reasonable price for your electricity and being able to generate enough electricity at the right time and then you know to enable you to get a contract.
Andrew Gardner: And of course you will need an export license.
Andrew Geens: Yeah, okay, thank you.
Q) Does CHPQA provide any advantages for biogas CHP in Northern Ireland?
A) Andrew Gardner: Yes. The advantages used to be a little bit more, there used to be enhanced capital allowances on new projects but unfortunately, that disappeared on the 1st of April this year. So apart from the supply of electricity and the supply to heat, there is also still an opportunity for preferential business rates if those apply to the project.</>
Andrew Geens: Thanks Andrew.
Q) Next question is: are there some instances where electrically led CHP units are more efficient?
A) Chris Marsland: I wouldn’t say they were more efficient, I think there are opportunities out there for electrically LED CHPs. I think it’s driven by the cost by the spark spread for the customer but yes I’ve looked at installations where electric-only generation does actually work. It sort of in some ways goes against the principle of CHP and you know saving emissions and reducing carbon but it’s possible yes.
Andrew Gardner: What you have to be careful about is that you must have some heat usage, otherwise, if you’re just purely electricity and no heat, then it is unlikely that the CHPQA would class that as a CHP unit especially if you’ve got zero heat because effectively you’re just using it as a generator.
Andrew Geens: Yep, okay thanks. I’ve got a few questions I think have come in before you’ve answered about the electricity carbon factor so I’ll skip over that.
Q) Is CHP eligible for RHI grants?
A) Andrew Gardner: Yes they are. There is an RHI uplift still available but again it is dependent upon having your CHP unit registered with the CHPQA program. So yes there is an RHI incentive but more information regarding that can be found on the CHPQA website.
Andrew Geens: Thank you.
Q) Sort of related I think: is biomethane a good way to boost this technology?
A) Chris Marsland: Okay I think from my perspective, I would say that it depends on the volume of biomethane you have available. I think if you have a lot of biomethane available the answer is probably to inject it into the grid, clean it up, scrub it and inject it into the gas grid. I think if you’ve got a lesser amount available then a CHP is a good way to lower the carbon footprint and to make use of that without too much expense.
Andrew Gardner: And also there can be additional maintenance costs especially if the quality of the gas is not up to that which is expected. Most CHP contracts do have a specification for the gas into it otherwise if you have biomethane that is, what we’d say, slightly wet then this can become acidic and reduce the engine life.
Chris Marsland: Yeah a lot has a lot to do with the feedstock that’s producing the biomethane, Andrew’s spot on.
Andrew Geens: Okay, thanks.
Q) Someone’s just asking for a repeat of the emission factors you said should be used for gas and electric. I’m not sure there was a single figure but can you just repeat some of that?
A) Andrew Gardner: Yeah the figures that I used in my presentation, came from the 2014-2015 CRC values and as I explained, and Chris also went on to state that the factors nowadays have changed and where possible you should use the factors as Chris mentioned.
Chris Marsland: I think all I would add is as I was saying at the time there’s a whole range of emission factors that you can choose depending on almost what answer you want, I think the ones that I’ve been using more recently are the HM Treasury Green Book emission factors as I think, whilst they sit somewhere in the middle of the range, but at least it can be consistent and it’s a government factor that it is harder for people to disagree with.
Andrew Geens: Okay.
Q) What is the typical life of a CHP and how does the maintenance cost fare over the life’s CHP unit?
A) Andrew Gardner: It depends on regular maintenance. I’ve come across the CHP’s that have been in use for 25 plus years now and still operating perfectly adequately.
Chris Marsland: I would concur with that, I think they can be like triggers broom, those of you that are familiar with Only Fools and Horses, you can replace virtually all the parts over a lifetime and, as Andrew says, 25 years later they can still be operating.
But the maintenance costs, likewise as Andy alluded, to earlier it depends how long you take your maintenance contract out for. There’s normally a large maintenance bill on a CHP towards the end of 10 years operation, typically 10 years, so if you take out a maintenance contract for 10 years and are clever about it that normally gets wrapped in so you pay a tiny little bit extra for every hour that you run but you’re covered at the end of year 10 so you get a nice fully refurbished CHP.
Andrew Gardner: Absolutely, and the other thing you should always take into consideration is that technology moves on. When I first started looking at CHPs we were looking at you know 30 to 32 percent electrical efficiency. Now, these are anywhere up between 35 and 38 percent. So as technology moves on, you may wish to update your CHP unit or replace it entirely and this can be included within the maintenance package.
Andrew Geens: Okay, thanks. we are running out of time. Just two questions I think I’m going to squeeze them in.
Q) One, is there are some DNOs that will oppose CHP in some areas, do we know why this is and whether it can be overcome?
A) Chris Marsland: I would hesitate with the phraseology, but yes there are challenges to connect generation into certain areas of the DNO networks and unfortunately it’s just something we have to work together with the DNOs on. They’ve had massive growth, and rightly so, of renewable electricity going into their networks which is causing them problems and their concerns and their issues are very valid. As embedded generation suppliers we need to work with them to come up with the best solution.
Andrew Geens: Last question:
Q) Okay well a nice philosophical question to end on: if we’re heading towards a NetZero future, well we are heading towards a net-zero carbon future, how far into the future do you see the benefits for CHP to be around?
A) Andrew Gardner: Umm gosh.
Andrew Geens: Bearing in mind you were talking about both financial and carbon benefits.
Andrew Gardner: Yes, certainly if the spark spread is maintained then yes there will always be financial benefits and also, you know, it depends if the incentives are still with it, like climate change levy exemption. Because that is, even though the electricity is to be frozen, the gas is continuing onwards and upwards. So there will always be a financial benefit. the carbon savings yes, they may be reduced, but I think you’ll always find there will be some and of course, as technology moves on then we might find different fuels for CHPs.
Chris Marsland: And I’ve got a really long answer which I’ll try and truncate, Mr. Geens.
I think it all depends on how decarbonising of heat is treated. If the decarbonisation of heat goes down the line of hydrogen injection into the national gas grid, then I think there is a long and healthy future for CHP. If it doesn’t I think, I agree with Andy, there is still a future but it will tend to be a little bit more niche and will be driven solely by the financial benefits and maybe would be looking at post-treatments of the exhausts wrapped into that.
Andrew Geens: Okay, Thank you very much.
Thank You
I’d just like to finish by thanking both of you for presenting today, I think the number and variety of questions suggest the audience found that informative and interesting as well. So thank you all for registering in for this webinar. I look forward to seeing a few of you at the June ones and keep yourselves safe in the meantime thanks all.
Andrew Gardner: Thank you.
Chris Marsland: Thank you.